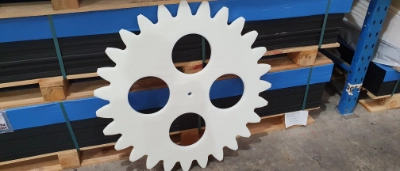
What is a Plastic Gear?
Generally made from Ertalon 6PLA or Ertacetal C, gears are toothed mechanical components to transmit motion and power. Even though plastic gears can be paired, for the best wear life performance pairing with another non-plastic (general steel) gear is ideal.
Benefits of Plastic Gears vs metal gears
- Eliminating Lubricants – Due to the low friction and lubricity properties of plastics, it is often possible for plastics gears to operate without lubrication.
- Dirty & dusty conditions – plastics tend to be more tolerant to non-ideal conditions, such as dirty and dusty conditions, especially when external lubricants are eliminated.
- Low Friction – This reduces energy consumption due to lower driving forces, as well as contributing to longer service life.
- Reduced wear – particularly when plastics are paired with steel, the wear on both materials are lower than metal-on-metal and plastic-on-plastic.
- Sacrificial – plastics can be used a sacrificial component in a drive system, to protect other more expensive parts being damaged in the event of system failures or jams.
- Fatigue – Plastics don’t suffer from fatigue in the same way that metals, but materials such as Nylatron MC901 can provide additional resistance.
Dotmar has qualified engineers that can provide direct support with plastic gear material selection and recommendations.
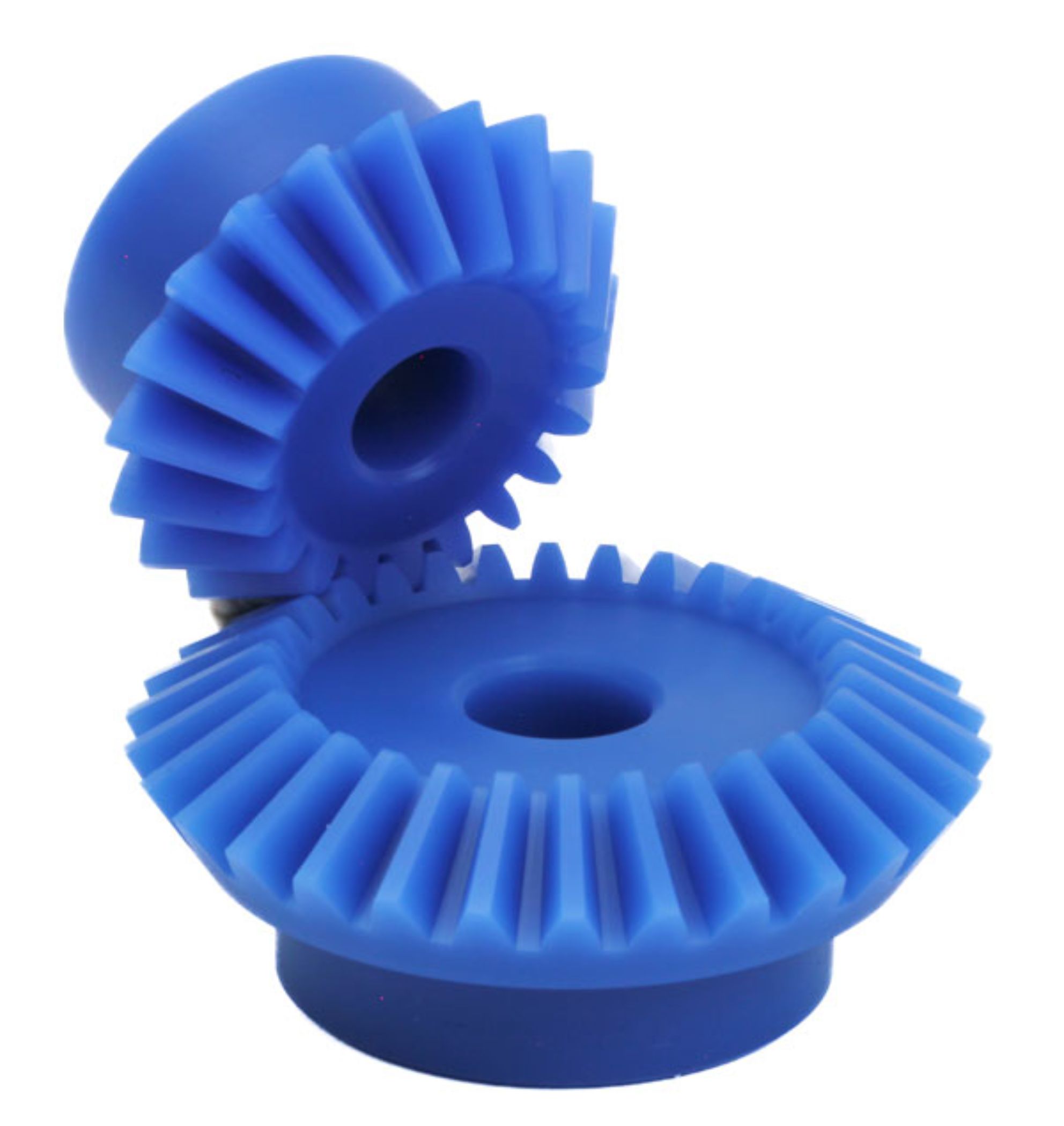