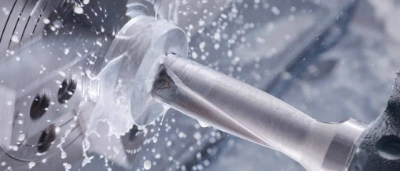
Firstly, keep it cool
Due to poor thermal conductivity and lower melting properties compared to metals, the main goal when machining plastics is to avoid heat generation or build-up and evacuating the swarf. This avoids deformation, stress build-up and even melting.
Tips
- When machining nylons, UHMWPE, and softer materials, go for maximum feed and speed to get the swarf away from the tool and avoid swarf build-up or wrap-around.
- Select tools with large clearance to allow swarf evacuation and deeper cuts.
- Air blast or vacuum ventures may assist.
- High-Speed Steel works well, but solid carbide is stiffer.
- For glass or carbon fibre-reinforced materials use carbide, reduce speed, and increase feed rates.
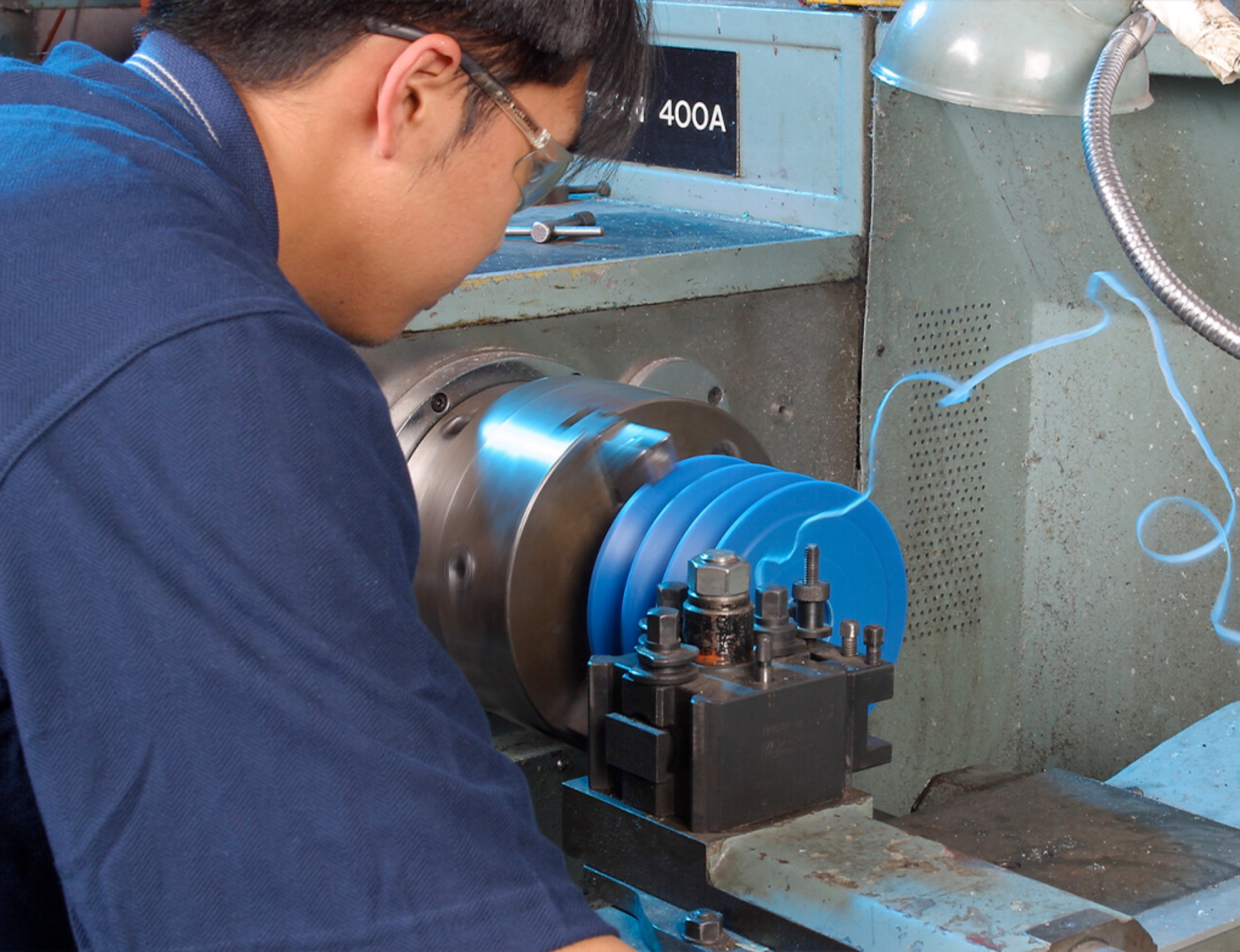
Even though coolants are not generally required for most plastic machining, they are recommended for drilling and parting. To achieve optimum surface finishes and close tolerances a water-soluble coolant is suggested. Mineral oil-based cutting fluids are suitable for many plastics but may contribute to stress cracking of amorphous plastics such as polycarbonate, PSU, and PEI.
When using coolant on amorphous materials wash immediately in isopropyl alcohol and pure water post machining.
Drilling
Plastics can build up heat very easily during drilling operations, especially when hole depths are greater than twice the diameter, therefore a cooling liquid is generally required.
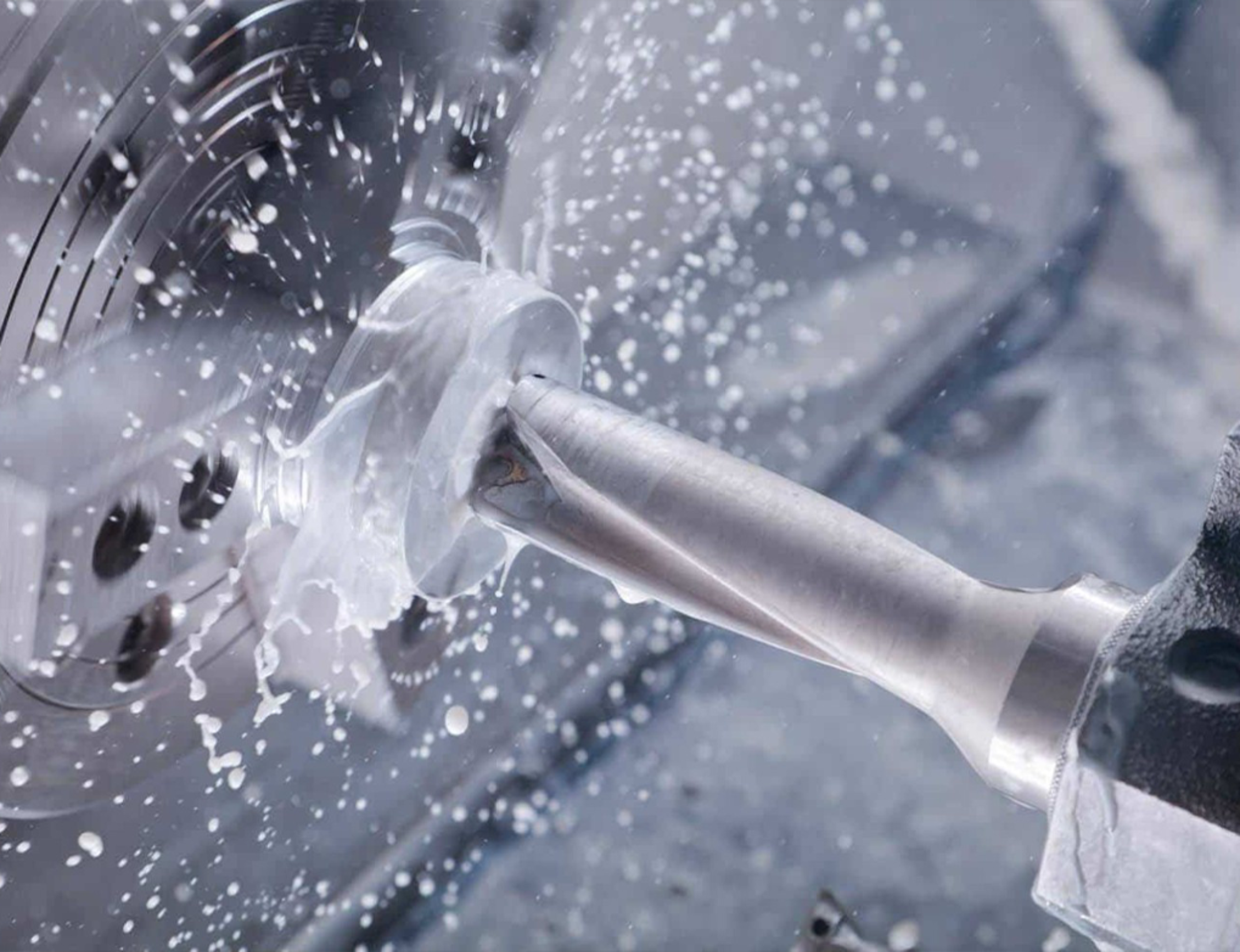
Small diameter holes (0.5-25mm diameter)
High-speed steel twist drills generally work well. In order to improve heat and swarf removal, frequent pull-outs (peck-drilling) are necessary. A slow spiral (low helix) drill will allow for better swarf removal..
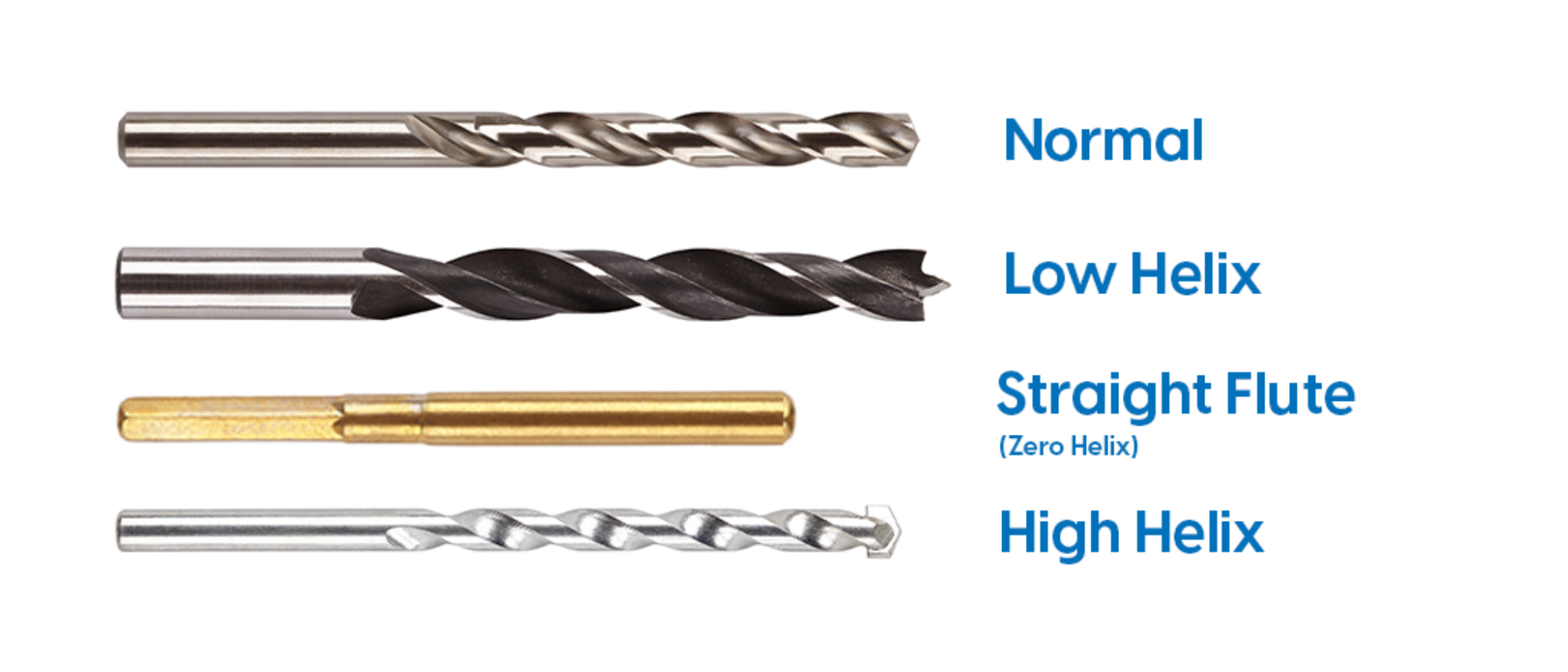
Large diameter holes (25mm diameter & larger)
It is advised to use drills with a thinned web in order to reduce friction and hence heat generation. Drill large holes stepwise: for example, a bore diameter of 50mm should be made by drilling successively with Ø12mm and Ø25mm, then expanding the hole further with larger diameter drills with a single boring tool.
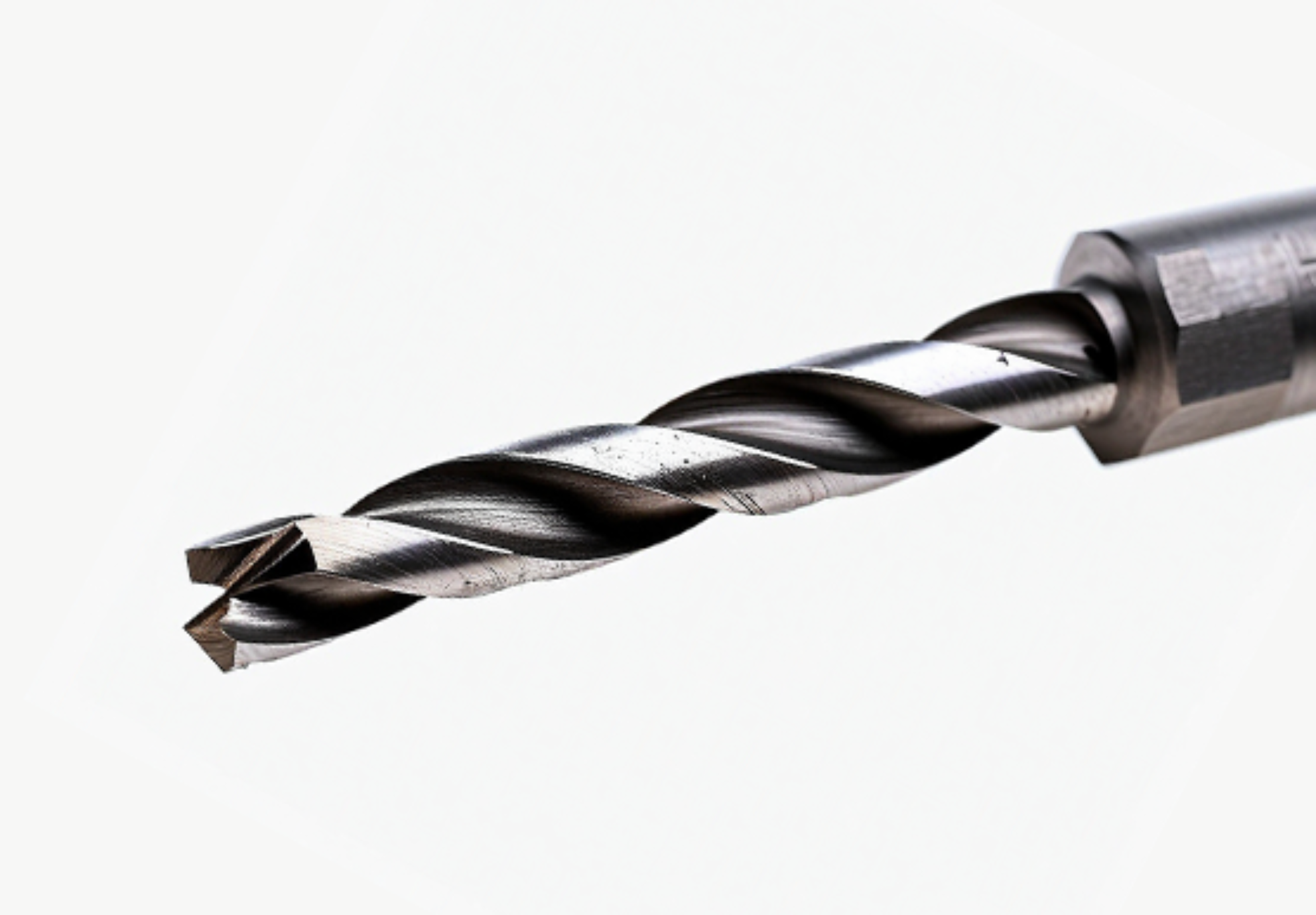